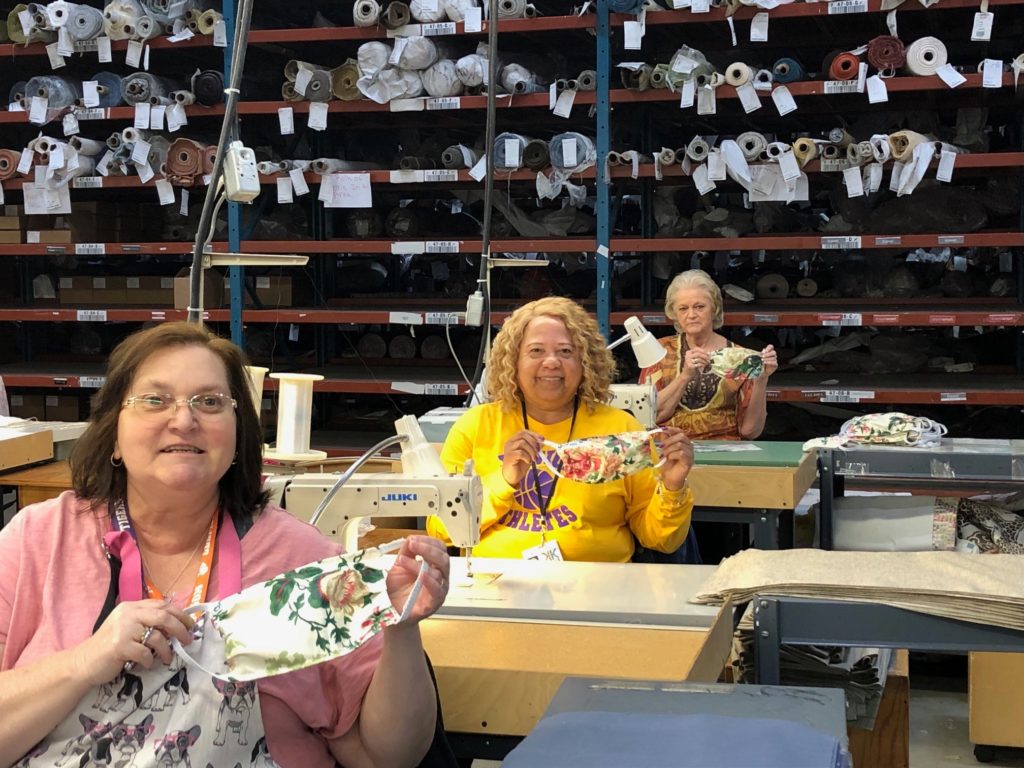
The Great Masking: Designers Collaborate to Fight the Pandemic
Editor’s Note:
Over the past two weeks, Covid-19 has descended like a pall over all of our day-to-day realities, shuttering schools, prohibiting movement, and pretty much grinding the economy to a halt. At Designer Pages Media, we’ve done our best to go about business as usual, but—as nothing is as it used to be—we’ve decided to acknowledge this new reality and begin running stories on how the pandemic is affecting the design community. There’s lots of news to share, some of it encouraging, some of it less so. Thankfully, our first piece is of the latter variety. Check it out below.
Designers and textile manufacturers from East to West are mobilizing in a widespread effort to make Coronavirus Masks. Turns out that thread, sewing skills, and initiative go a long way.
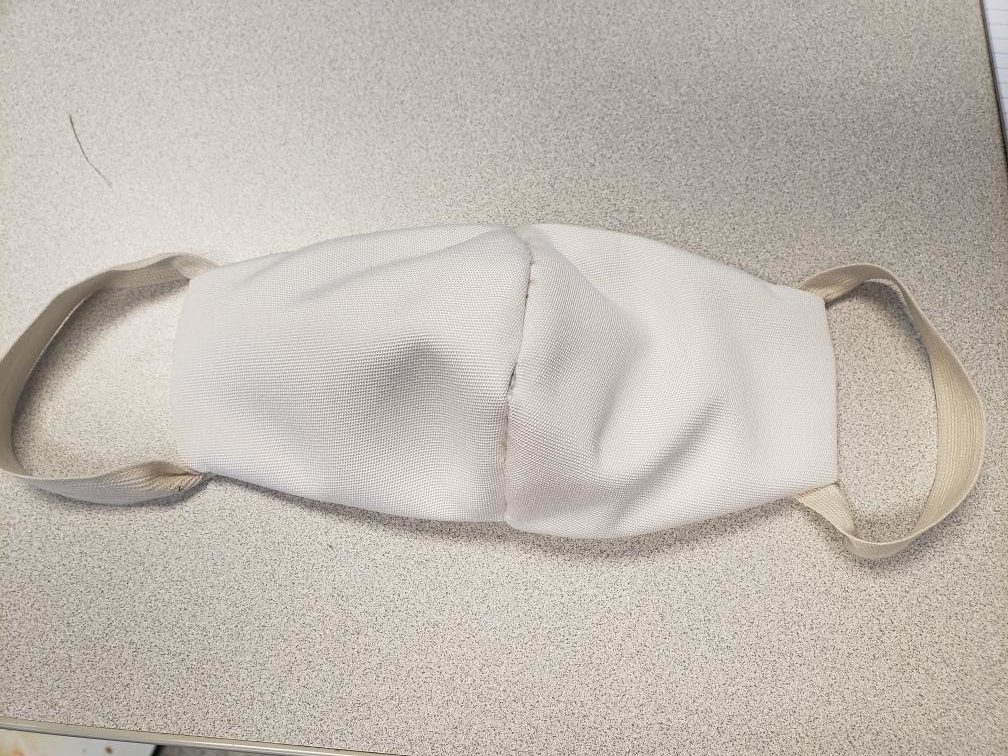
One of the first to utilize the tools of her trade to make surgical masks, Designer Jean Liu responded to the entreaties of medical personnel by mobilizing Woodard Furniture, a Michigan-based company, to create masks utilizing a simple DIY design: “I texted it to our plant manager at 11 p.m. and by 9 a.m. the next day we had a prototype ready to go.”
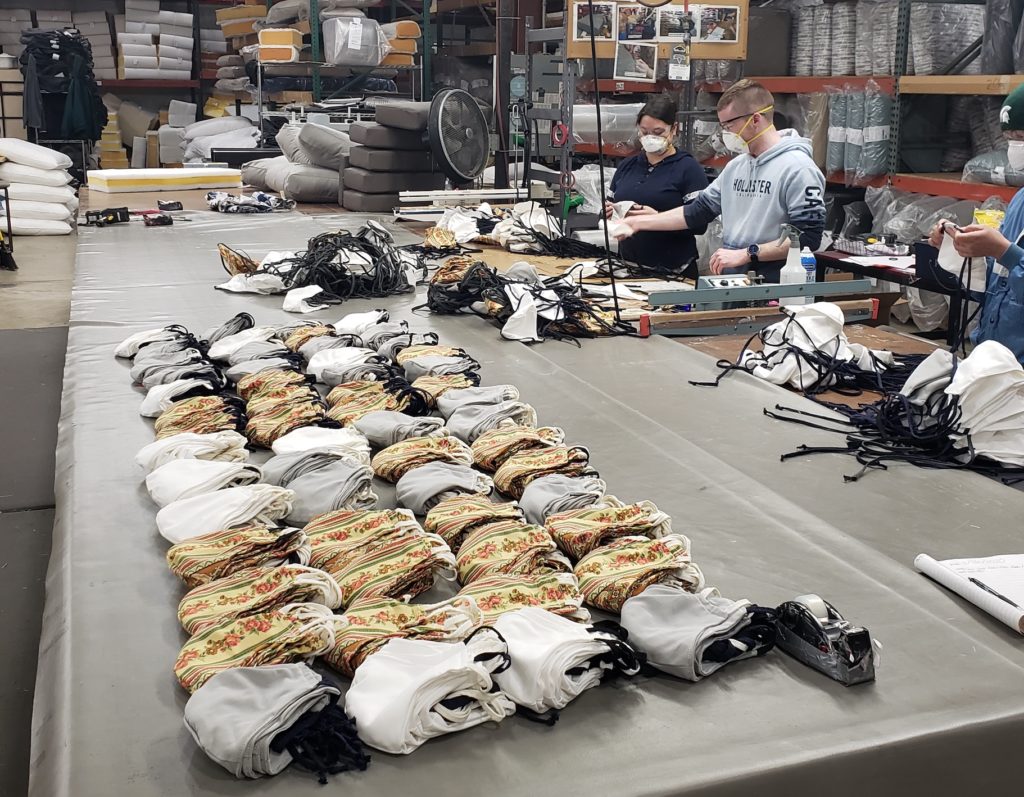
These aren’t the medical-grade N95 masks we’ve heard so much about, but rather protective masks designed to be worn over those, thereby protecting and preserving a precious resource. But they can be used in a pinch, in cases where healthcare workers have no masks at all—as they’re much better than a bandana.
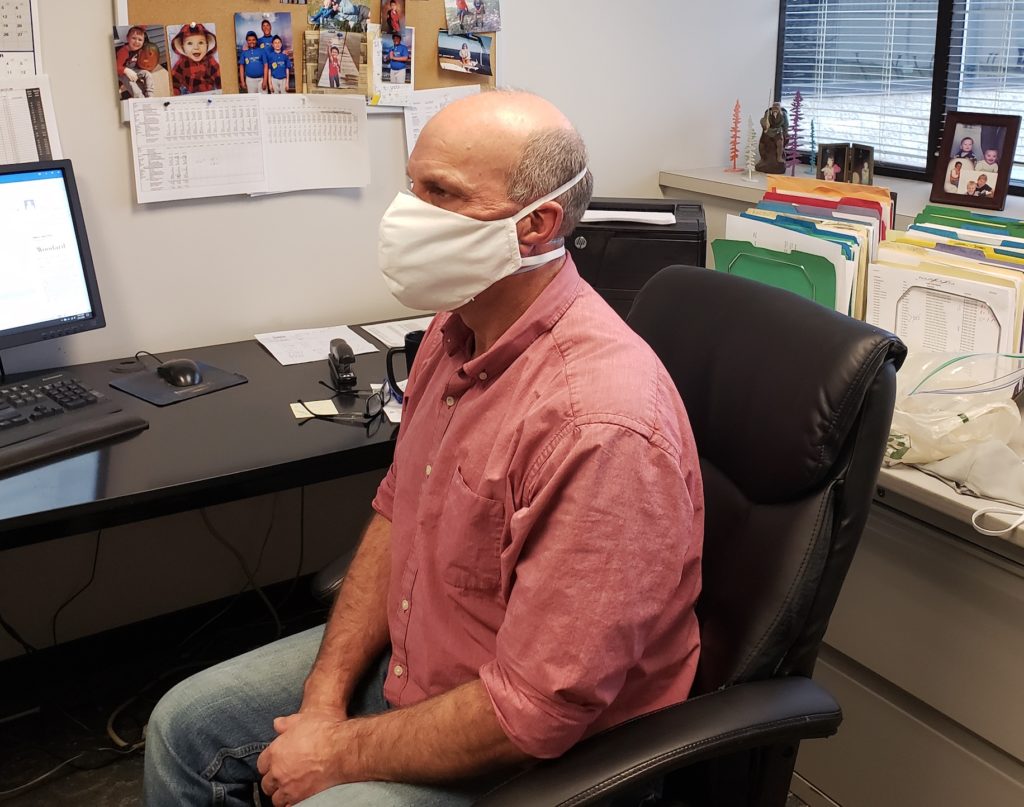
Liu also recruited others to the effort, including North Carolina-based Wesley Hall Furniture and textile giants Kravet and Schumacher. Together they can make 10,000 masks a day. And Kravet has expanded the effort into a coordinated recruitment response, donating 3,100 yards of fabric to manufacturers who are re-tooling to make masks, including the aforementioned Woodard Furniture.
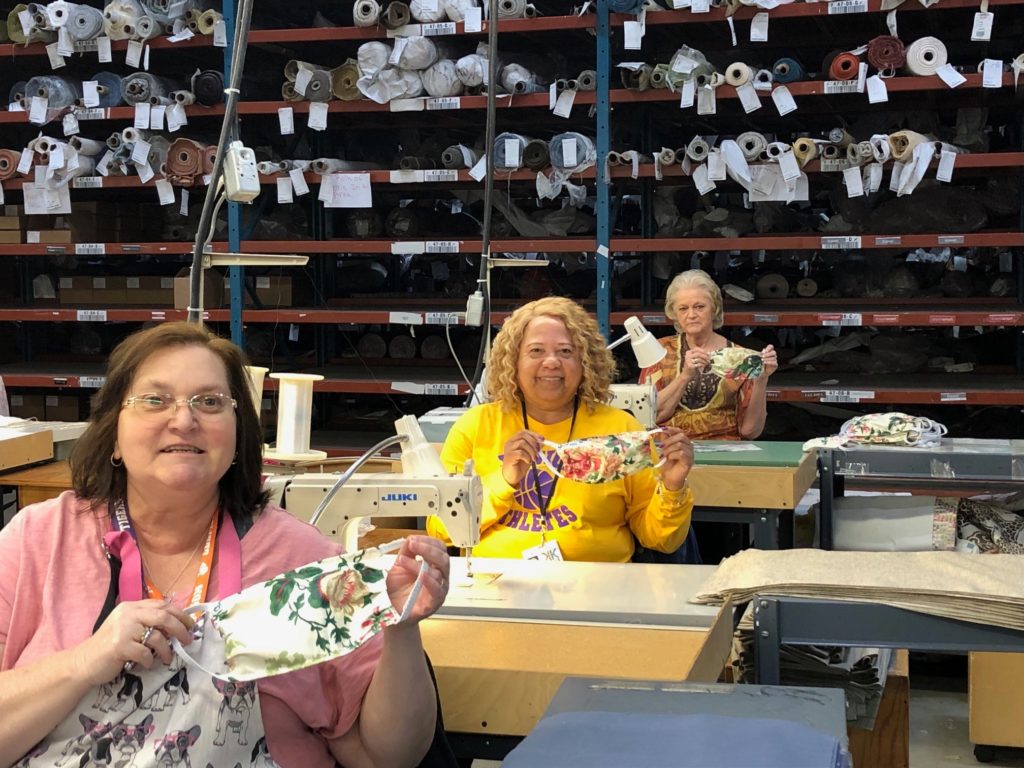
Kravet is also working on using materials besides cotton—whose shortcoming is that it can only be used once—employing alternatives like plastic and synthetic fabric. “We’re going to experiment and try to make those into masks,” says Co-Principal and Executive VP Ellen Kravet Burke, “We think we’ll be able to do it.”
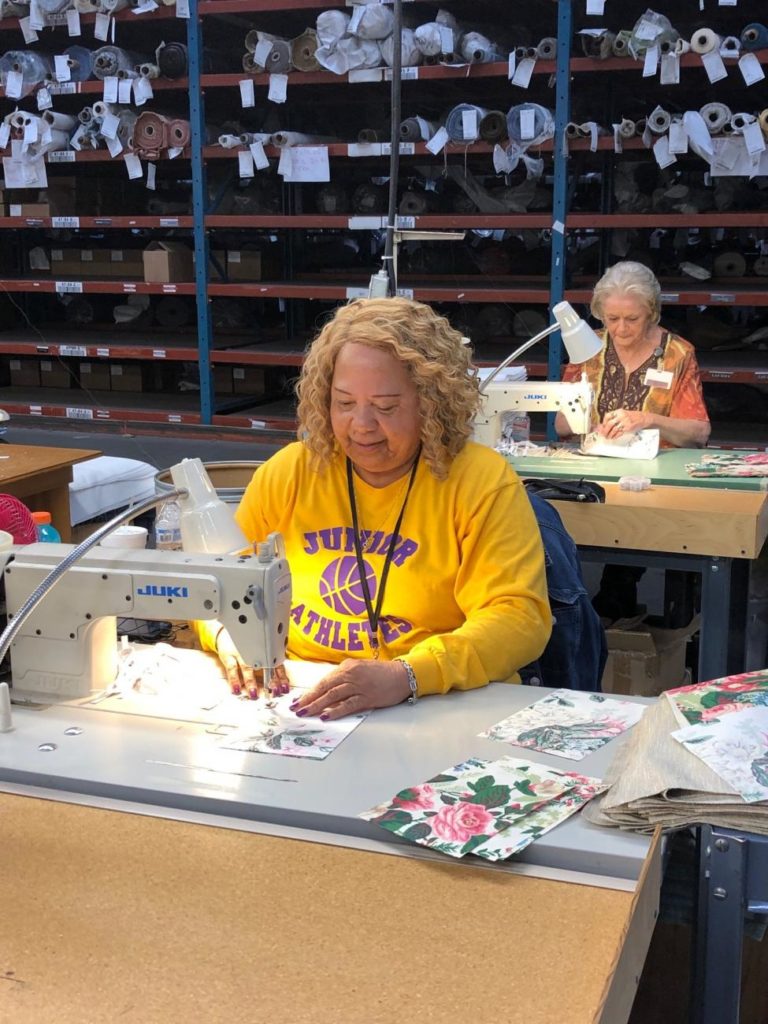
On the West Coast, Seattle’s kaas tailored entered this effort early by halting all furniture and upholstery production to focus exclusively on face masks and face shields, while also partnering with Providence Healthcare on the 100 million mask challenge. A couple of days into this effort, kaas tailored was making upwards of 4,000 masks and 800 shields daily. They’ve also posted the mask and shield specs on their website for other manufacturers and citizen volunteers to join in the effort.
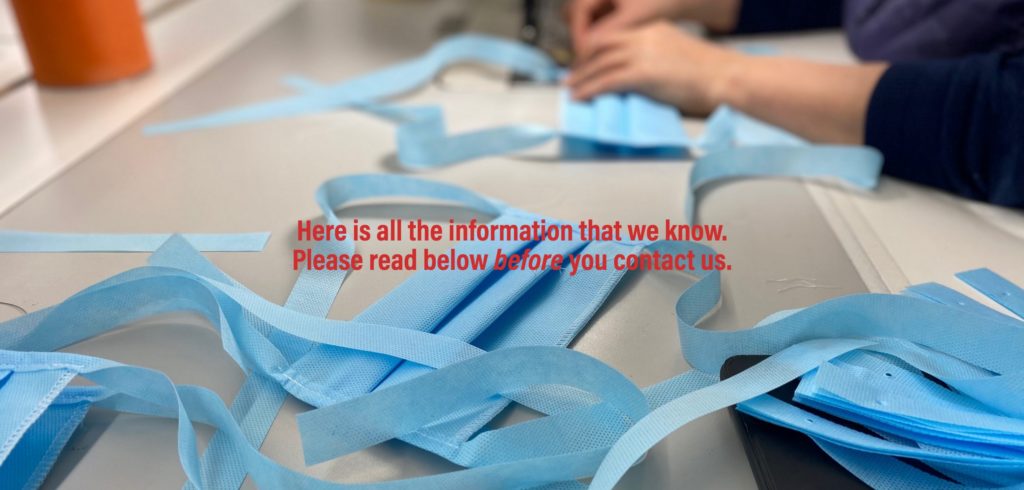
N.Y.’s Stitchroom is contributing too. They’ve established a Facebook Group to solicit donations of materials, and they’re conducting an outreach effort to get anyone with a sewing machine to help by following extensive online instructions, including DIY videos and a comprehensive mask manual PDF: “All masks are going to hospitals who have reached out to us in need of extra PPE. These masks are intended to be used for lower-risk patient care situations to make N95s more readily available for high-risk care, but may also be used as a last resort if there are no PPE.”
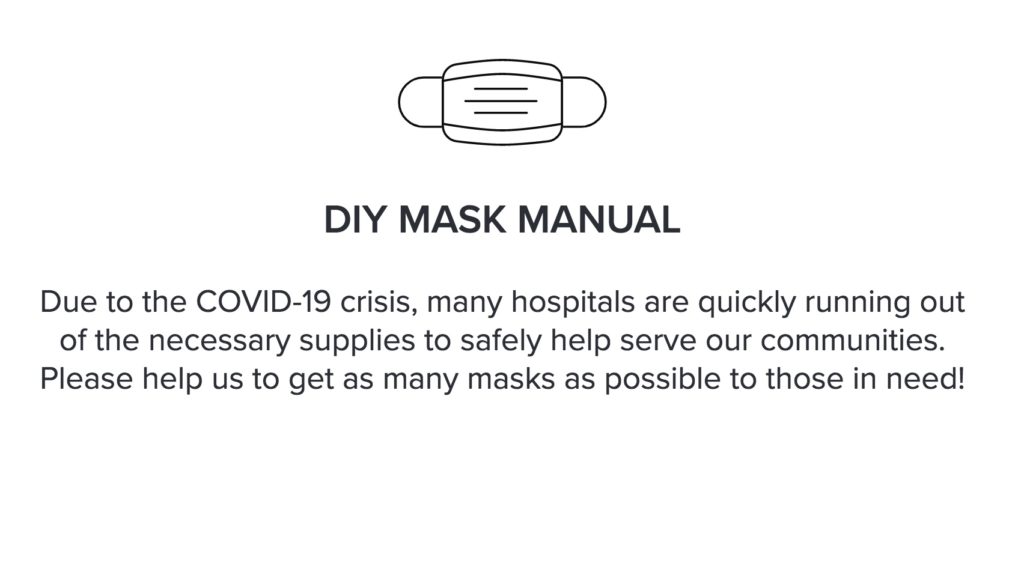
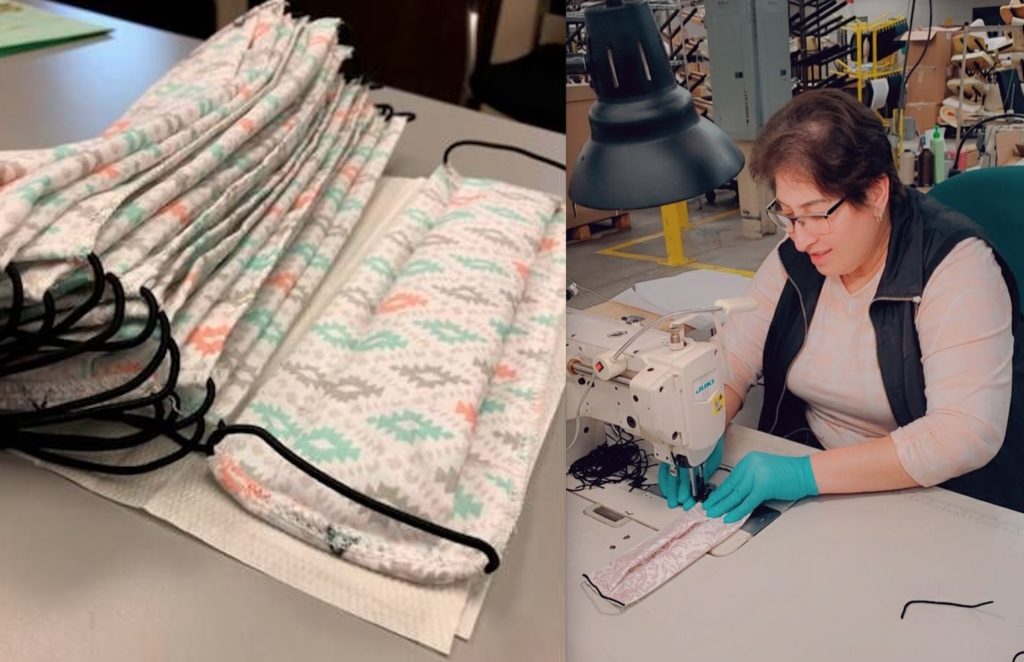
And across the river in New Jersey—which has reported the second largest amount of positive cases—manufacturer Stylex is producing washable protective masks. Company CEO Bruce Golden is personally involved in the effort, hand-delivering masks to local hospitals and healthcare facilities: “We are honored to serve our community in this time of crisis, and putting our amazing artisans to work on this task is a labor of love and solidarity.”
Leave a Reply